In multi-bed reactors, the process may require a cooling phase between two beds. This can be achieved by injecting a fluid, which is then collected, mixed, and redistributed over the subsequent bed.
Custom design tailored to the application, or detailed design per specifications, ensuring no interference with other reactor internals.
Mechanical design that limits deflection during operation.
Fixing devices designed to secure each panel of the tray assembly.
Tight manufacturing tolerances to ensure panel flatness.
Gaskets to prevent liquid leakage through panel joints.
Trial assembly at Ekaislot shop as a standard control, with a report assessing whether the given dimensions match the vessel's as-built dimensions.
Technical assistance or on-site supervision services provided by Ekaislot to ensure proper installation and application of all required precautions.
Application: Hydrotreating, hydrocracking, hydrogenation.
Design based on your application
The mixing system consists of a horizontal collection tray, a mixing chamber located beneath it, and at least one passage extending through the collection tray into the mixing chamber. Together, the collection tray and mixing chamber create a two-phase mixing volume. The passage allows fluid to flow from above the collection tray into the mixing chamber, which is equipped with at least one outlet opening for the downward flow of fluid.
The mixing of quench fluid is notably enhanced when the quench is introduced into a region above the collection tray. The injection direction is carefully chosen to promote rotational flow on the collection tray, improving the mixing process.
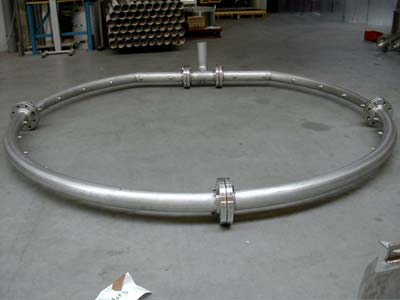
Quench injection ring
| 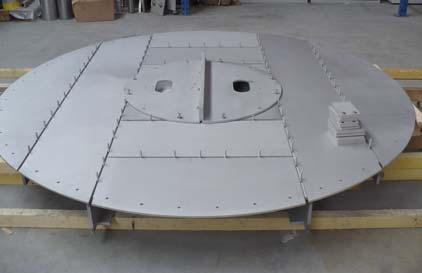
Collection tray and mixing chamber |
Design Parameters
Process parameters:
Key process parameters include design and operating temperature, liquid and gas flow rates with their physical characteristics, and the pressure drop through the quench injection. Since quench design is critical for process performance, the process licensor defines the type, quantity, and configuration of spraying nozzles (such as a simple ring pipe or a header with laterals). Additionally, the collection tray design must determine the quantity, shape, and cross-sectional area of outlet openings. The size and shape of the mixing chamber are also determined by process parameters, particularly as residence time impacts mixing efficiency.
Mechanical parameters:
Manhole size, maximum liquid height on the tray, acceptable tray deflection, and corrosion allowance are critical mechanical parameters used to determine the necessary reinforcement.